Using masts to reduce energy expenditure in the maritime industry
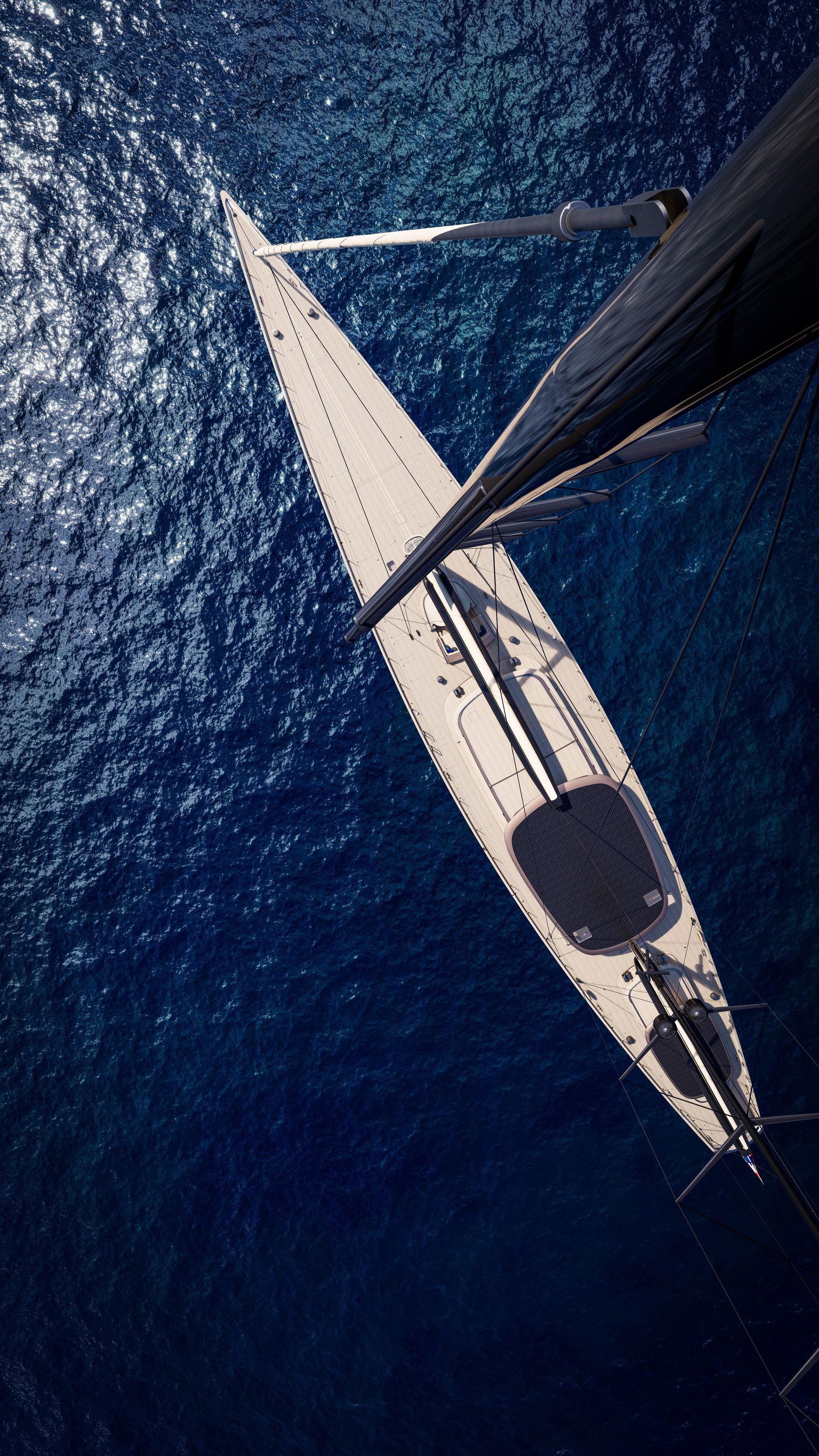
When you’re operating outside of the grid, energy balance is vital. Without easy access to power, systems need to be balanced, ensuring that more energy is coming in than out. And if you have to generate that power yourself? From the local environment? Then this issue is further intensified.
One way of countering this is by, of course, generating more power, but this often isn’t enough. Instead, the goal is to look at systems that use a lot of energy and work out how to streamline them.
For example, on yachts, one of the biggest energy expenditures are hotel loads, with a focus specifically on cooling and ventilation. Air conditioning units take up a huge amount of energy when sailing, so anything that can be done to reduce their load is hugely important
To deal with this exact issue the team behind Sailing Yacht Zero, a world-first vessel powered completely by renewable energy, came up with a novel concept: using the mast as a ventilation system to help save energy.
How does this work? Well, we spoke with a range of people working on the project to find out.
The genesis of an idea
Bob van Someren, a physicist, explains that when the team approached something like Sailing Yacht Zero, they spent a lot of time examining systems that used the most power. “And one of the biggest expenditures is the air conditioning system,” he says.
For the comfort of those onboard, this sort of temperature regulation is vital, but the team spotted an interesting opportunity in how this system works. When an area is being air conditioned, it must also be ventilated, ensuring there’s fresh air in the system and any moisture is managed — and here’s where it gets interesting.
“If you ventilate, you also blow out the conditioned air,” Van Someren says.
In other words, energy is expended by physically expelling air that has been cooled or heated. That’s a lot of wasted power. The Project Zero team wanted to find a way around this. To begin with, they looked at a range of options, including using natural airflow.
One of these was what happens when a vessel is anchored. “It’s always in line with the wind,” Van Someren says, “that means you can use the wind as it passes over the deck to create a Venturi effect.”
Effectively, this would use the principle that airflow speeds up when it’s passed through a constricted area. This creates a low-pressure zone that draws in air, which could be used to create a ventilation system. After some careful analysis, it became clear this was tough to achieve on a sailing vessel.
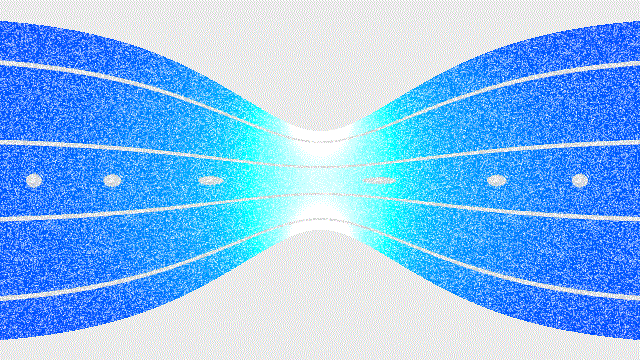
Yet as the team dived further into options, an interesting idea arose: what’s stopping them using the mast as a ventilation system?
Exploring whether a mast could ventilate a boat
“If you look at the mast, it’s basically a big chimney,” says Eduard van Benthem, the project manager of Project Zero. He explains that as the team were pondering how to ventilate the vessel, they couldn’t see a reason why putting a channel through the mast wouldn’t work. In fact, it might be precisely the energy-saving solution they were after.
The key part of ventilation is moving a mass of air. As the inside of a yacht warms, it’s this heated air that the team needs to move. Yet, because hot air naturally rises, some of the team pondered whether this could be routed up through the mast, a form of stack ventilation.
Following this revelation, Van Someren proceeded to explore the theory. “I did some calculations on it and it looked very doable,” he says.
The question, though, is whether the amount of ventilation power the mast provides is enough.
As Van Someren explains, when the sun shines on the dark-coloured mast, “it puts a certain amount of solar power on it, and that heat diffuses to the inside of the mast and heats up the air. That’s the power that drives the air upwards.”
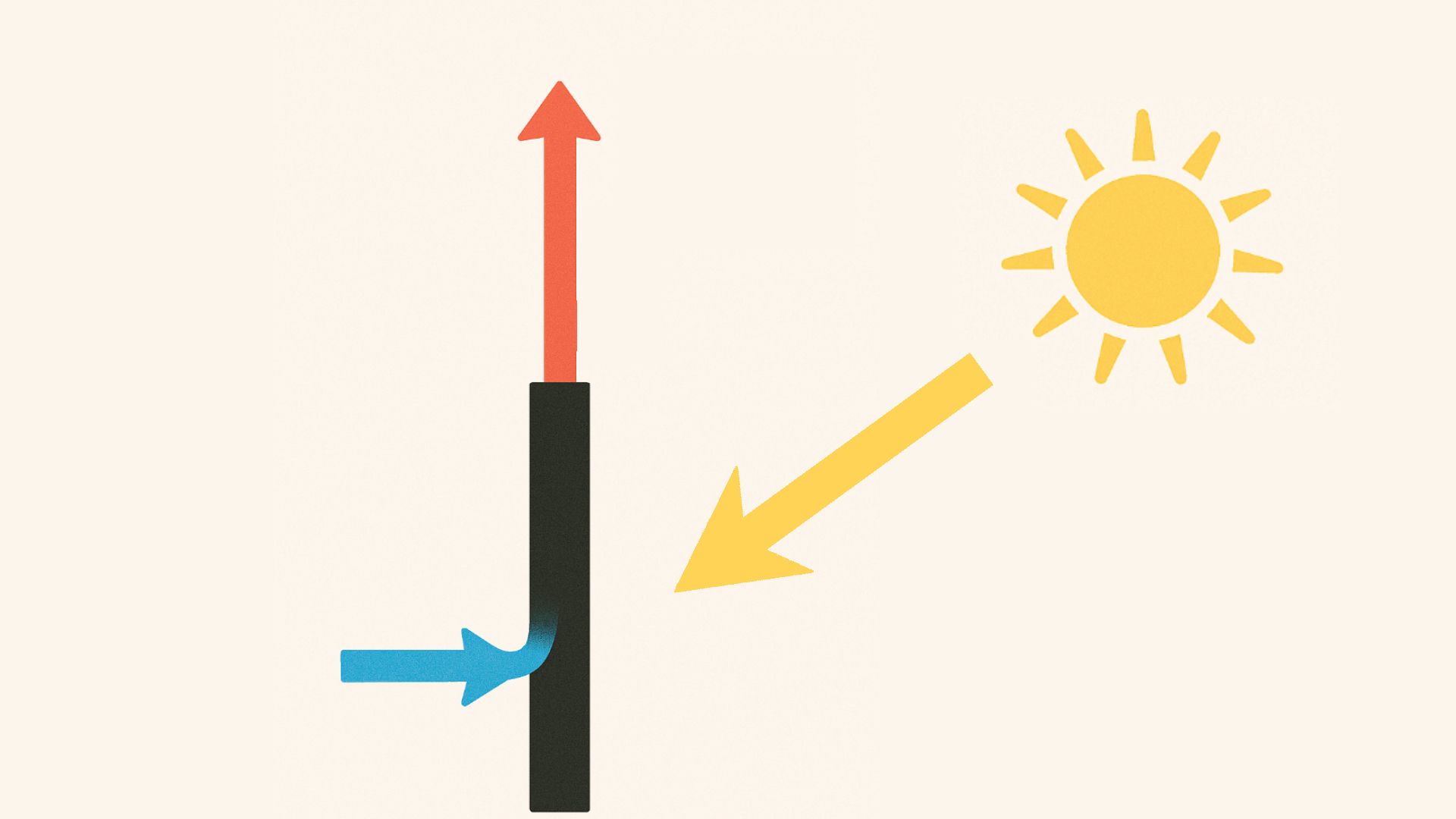
After doing some work on how much power this generates, Van Someren estimated it could generate 5-10 kW depending on the weather, something he describes as “a considerable amount,” and more than enough for this specific purpose.
As a comparison, a large fan would use a 1 to 1.5 kW motor, meaning the potential power this mast ventilation system could provide should be more than enough to meet Sailing Yacht Zero’s goals.
On paper, the concept works, but the team needed to see if a mast with a channel through the middle of it could be built and whether it could remain within the weight budget of the vessel. With that in mind, they met with Carbo-Link.
Connecting with Carbo-Link
When it comes to getting a mast built for a vessel the size of Yacht Zero, there are minimal options on the market. As the mast will be around 70 m long, this requires a specific and dedicated manufacturer, and isn’t something that’s possible to buy off the shelf — especially if there’s to be a channel down the middle.
Van Benthem explains that constructing a mast with an “open internal structure” is a “big challenge,” and something that many companies weren’t willing to take on. But, after further exploration, the team approached Carbo-Link.
“I like to think of it as a 25 year old startup,” says James Wilkinson, the programs and sales director of Carbo-Link. The company is an advanced composite manufacturing business headquartered just outside of Zurich. It combines material science, cutting-edge design, and engineering to provide structural systems for a large array of industries.
What really separates Carbo-Link though is the fact, as Wilkinson explains, it "not only designs, engineers and manufactures the final solution, but also the materials and production processes that are required to reach the end solution."
In other words, they build the things they design.
Carbo-Link maintains end-to-end control over the entire creation process, going from the initial concept through to construction and the post-work support. This includes design, finite element analysis (FEA), numerical simulation, 3D modelling, material engineering, and production. Everything is handled in-house.
This unique integration of material science, engineering, and manufacturing enables Carbo-Link to tackle challenges many would consider unfeasible — such as developing a mast with an internal ventilation channel, a feat never before achieved at this scale.
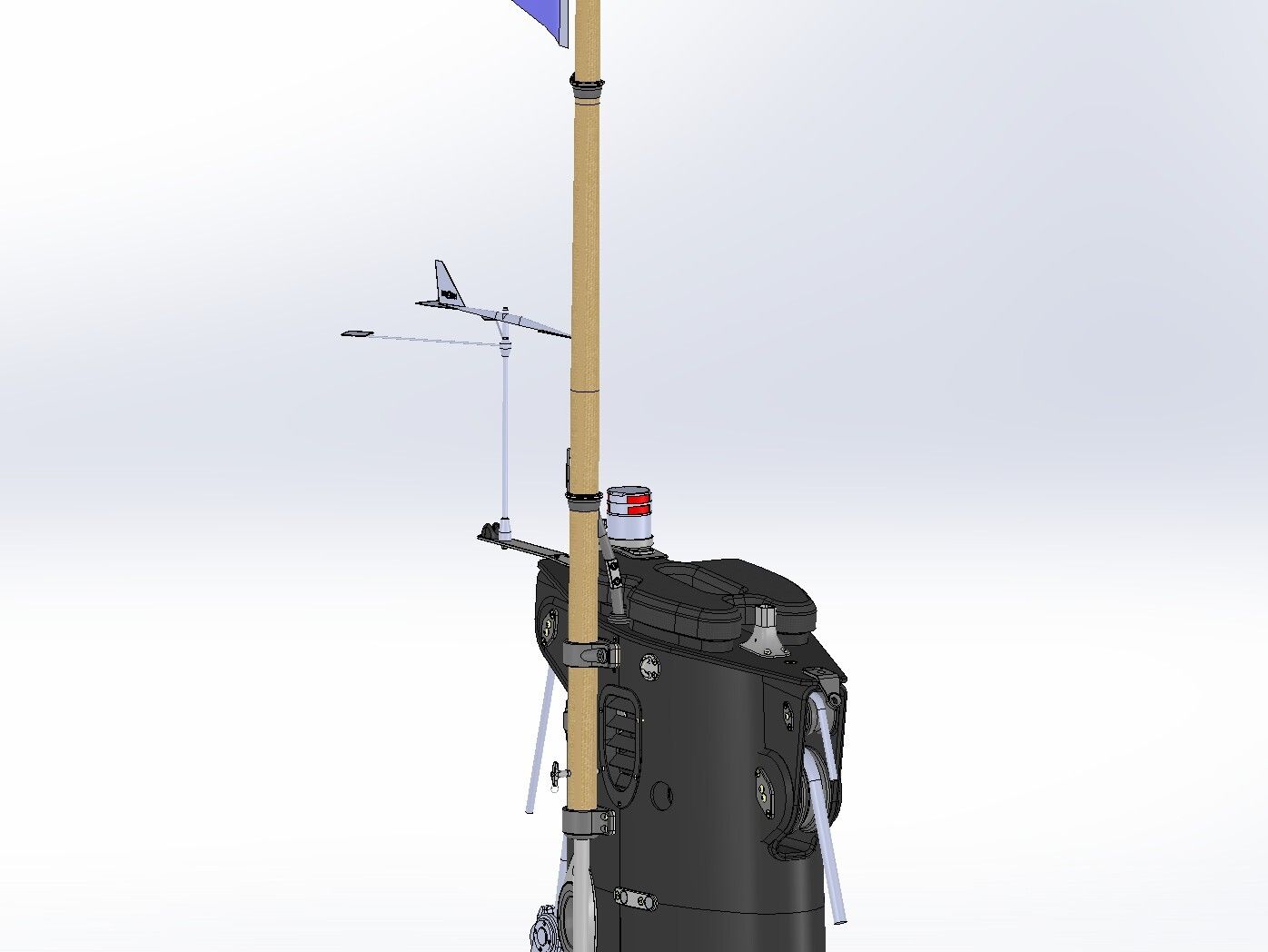
Turning physics into reality, and actually building the mast
“We saw an opportunity,” says Wilkinson from Carbo-Link. Here was a project that could kickstart an entire new business. But before they got there, the team had to grapple with the difficulty of actually building this mast.
To find out more about this, we spoke with Edoardo Volpe, the mast division development engineer at Carbo-Link who is coordinating the engineering process on this project.
“It’s not been done before,” Volpe tells us when discussing the ventilation system, but he was keen to start working on it, as he and the Carbo-Link team saw it as an impressive idea.
The first element was to fully understand the project. Sailing Yacht Zero wanted a mast that maintained the largest area available in the tube, meaning usual reinforcements, tie-rods, and attachments had to be removed. It was back to the drawing board.
Volpe explains that the biggest issue with designing this channelled mast were the "structural challenges.” A mast the size of the one on Project Zero must be able to safely operate in all weathers, meaning it needs to not only take a huge amount of force, but also have a level of flexibility to ensure optimum sailing performance. What makes it tougher is that, as aforementioned, this was new ground for mast design.
Thankfully, although this was new ground, it wasn't an entirely fresh approach.
“The integration of the ventilation channel does not change the principles of mast design,” Volpe says. There are some issues though, as “it drastically influences the structural design choices.”
Volple explains that in the design spiral, they “carefully investigated the forces acting on the mast and rigging structure, including forces transferred by the sails while sailing, or inertia (mass) forces in rough sea state.”
Rephrasing that, the structural design of the mast was created using the same environmental scenarios as other masts — but this time with a ventilation system running through the middle of it.
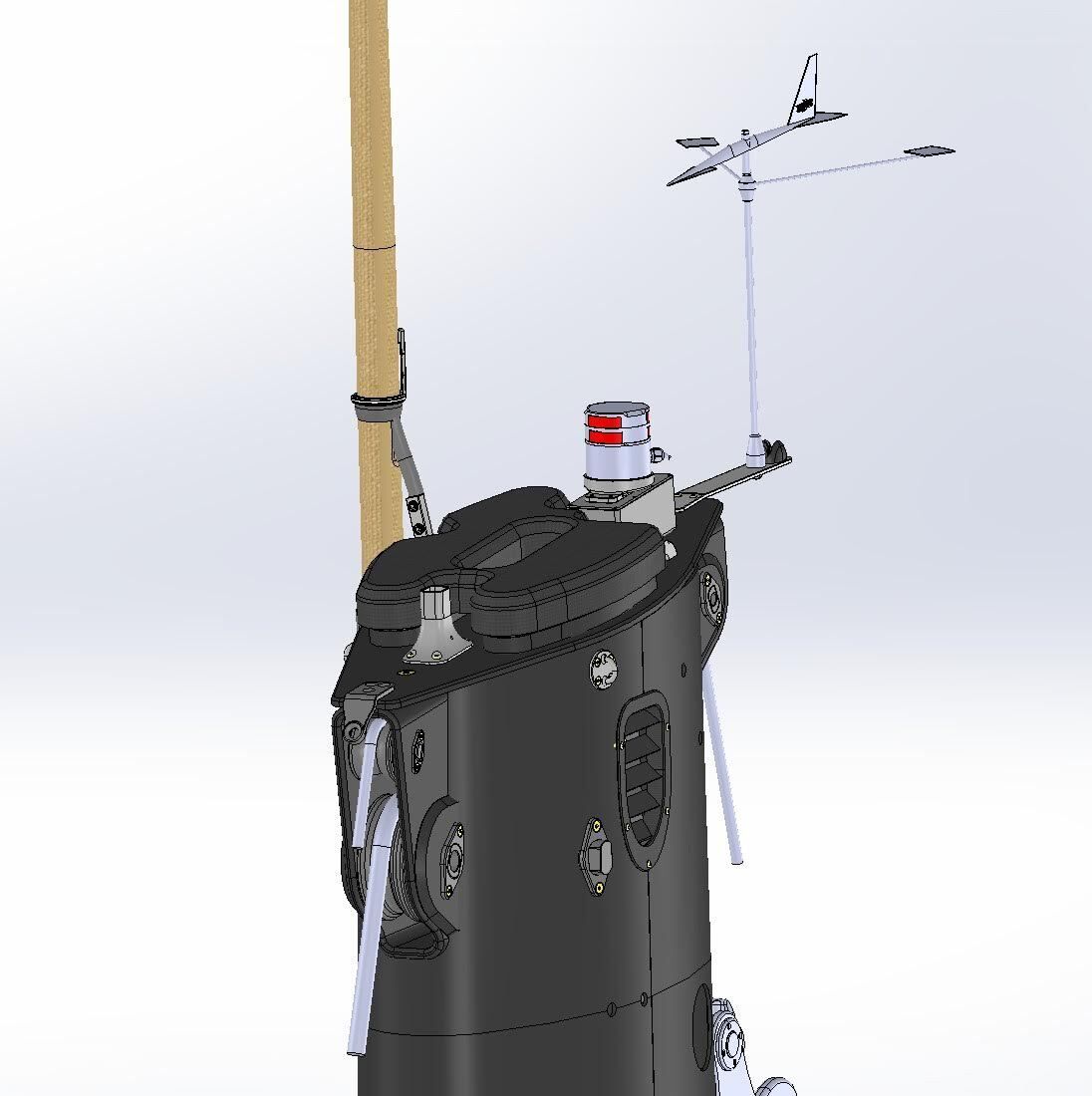
From this stage, Volpe says creating the hardware involved “a lot of structural design and fundamental modelling with some carbon fibre design.”
Hardly an easy task, but when combined with Carbo-Link’s holistic approach to design and construction, the team was able to complete this task.
What’s next for the mast ventilation system?
Project Zero will begin sea trials at the end of 2025. At this point, the first data from the mast’s real-world performance will be collected and analysed. From here, any changes that need to be made will be.
The most exciting element though is the inspiration this could deliver for the maritime industry. Cooling and energy balance is a huge issue on boats of all sizes, and this novel way of using the mast as a ventilation system is something a range of vessels can take inspiration from.
More so than though, this project shows the power of open thinking and collaboration. “For me the biggest future takeaway is that we shouldn’t take things for granted,” says Van Benthem, “always keep an open mind about improvements.”